TM 5-3895-376-14&P
Section II. REPAIR PARTS, SPECIAL TOOLS; TEST, MEASUREMENT, AND
DIAGNOSTIC EQUIPMENT (TMDE); AND SUPPORT EQUIPMENT
4-3. COMMON TOOLS AND EQUIPMENT.
For common tools and equipment refer to the Modi-
fied Table of Organization and Equipment (MTOE) ap-
plicable to your unit. The basic tool kit assigned to
mechanics for this unit is the Tool Kit, General Me-
chanics: Automotive as defined in SC 5180-90-N26.
All other tools required for the performance of each
task are listed in the setup of each task and identified
in Appendix F, Tool Identification List.
4-4. SPECIAL TOOLS, TMDE, AND SUPPORT
EQUIPMENT.
No special tools, TMDE, or support equipment are re-
quired for operation or maintenance of the plate com-
pactor.
4-5. REPAIR PARTS.
Repair parts are listed and illustrated in Appendix C
of this manual.
4-6. INSPECTION UPON RECEIPT.
Section Ill. SERVICE UPON RECEIPT
a.
Inspect plate compactor for loose or missing
mounting hardware on all components.
b.
Inspect around engine base for signs of oil leak-
age.
c.
Inspect fuel lines and fittings for signs of fuel leak-
age.
1.
Remove tape from exhaust on muffler and in-
take of air cleaner.
2.
Service the engine oil (Para. 4-12) and vibra-
tor oil (Para. 4-13).
b.
Perform before operation preventive mainte-
nance checks and services listed in section II of
chapter 2 and section IV of this chapter.
c.
Remove tag after adjusting tension on v-belt.
4-7. SERVICING UPON RECEIPT.
a.
Compactors shipped outside CONUS must be re-
moved from shipping crate and the following per-
formed:
Section IV. PREVENTIVE MAINTENANCE CHECKS AND SERVICES (PMCS)
4-8. GENERAL.
The necessary preventive maintenance checks and
services to be performed at the unit level are listed
and described in Table 4-2. The preventive mainte-
nance services include lubrication requirements for
the plate compactor, to be performed by unit mainte-
nance.
4-9. PMCS PROCEDURES.
The PMCS procedures are arranged in a logical se-
quence as indicated by the item numbers. Explana-
tion of column is in the PMCS table as follows:
a.
Item Number Column. This column lists, in logical
order of performance, the checks and services
that are to be performed. These numbers shall be
used as a source of item numbers for the TM
Number Column on DA Form 2404, Equipment
Inspection and Maintenance Worksheet, in re-
cording results of the checks and services.
b.
Interval Column. This column contains the time
frame for which a required check or service is to
be pet-formed.
c.
Location/Item to Check/Service Column. This col-
umn defines the item or group of items to be
checked and serviced.
4-4
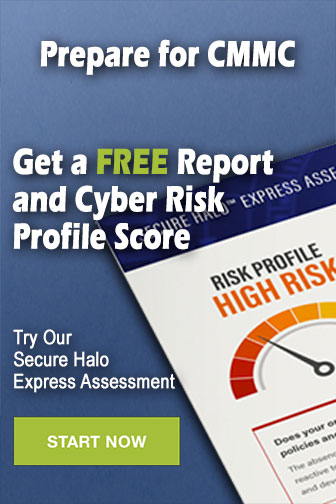